Статьи
Обзор наплавочных решений в промышленности
Доклад Урусова А. А. на научно-практическом семинаре к 100-летию выдающегося учёного-сварщика Петрова Л. Г. "Металлургия сварки и сварочные материалы" проведённом под эгидой НАКС на кафедре СПГПУ.
1. Износ как вызов экономике.
Износ деталей приносит ежегодные убытки в промышленности всех отраслей и всех стран мира. Счёт идёт на миллиарды долларов. Износ съедает не только те деньги, которые идут на закупку заменяемых деталей. Поскольку при остановках оборудования, связанных с его ремонтом, выпуск продукции на предприятии снижается, потери существенно возрастают. Время простоя – это потерянная прибыль! Ещё один глобальный вызов, связанный с износом – истощение природных ресурсов планеты!
По этим причинам повышение износостойкости, то есть продления ресурса деталей и увеличения межсервисного периода оборудования – есть важнейшая задача промышленных инженеров.
Мы сталкиваемся с износом почти во всех отраслях. Добывающие предприятия, строительство, деревообработка, химия, металлургия, машиностроение, везде в процессе работы изделия подвергаются следующим видам износа:
- Фрикционный износ типа «металл по металлу» возникает при трении качения и скольжения деталей относительно друг друга с недостаточным количеством смазки или совсем без нее.
- Ударный износ – при воздействии ударных или сжимающих нагрузок, приводящих к смятию и растрескиванию рабочих поверхностей.
- Совместный ударно-абразивный износ – при воздействии ударных нагрузок и режущего действия скользящих по инструменту твердых частиц, что приводит к выкрашиванию и стачиванию рабочих поверхностей.
- Интенсивный абразивный износ – в результате воздействия твёрдых минеральных материалов, приводящего к стачиванию и эрозии рабочей поверхности. Например, износ типа «металл по земле». Также разновидностью его можно считать эрозионный износ при воздействии на рабочую поверхность запыленного газового потока, или потока жидкости со взвесью.
- Коррозионный износ возникает в результате коррозионного воздействия химически агрессивной среды.
- Кавитационный износ имеет место в гидравлических системах, вызван воздействием ударных волн в жидких средах.
На практике реальный износ является результатом комбинированного воздействия нескольких указанных выше видов износа, иногда в сочетании с высокими температурами. Для снижения износа рабочие поверхности необходимо упрочнять. Термин «упрочнение» довольно распространён, хотя далеко не всегда борьба с износом сводится к повышению прочности. Подходя к решению задачи защиты, инженер должен определиться:
- с выбором способа нанесения покрытия (ответить на вопрос КАК?),
- с составом этого покрытия (ответить на вопрос ЧЕМ?).
Для принятия оптимального решения в первую очередь важно понять, какой вид износа превалирует. Также для выбора материала и способа покрытия необходим тщательный анализ всех издержек и определения экономической целесообразности такой работы. Игра должна стоить свеч, а овчинка выделки
2. Выбор способа нанесения защитных покрытий.
Существует довольно много процессов нанесения защитных покрытий на металлические рабочие поверхности, от практичной дуговой наплавки и различных видов напыления до пока экзотического лазерного плакирования.
2.1 Виды напыления.
2.1.1 Газопламенное напыление
Суть этого способа заключается в подаче наплавляемого материала в виде порошка в пламя ацетилено-кислородной горелки и напыление на предварительно разогретую до 500-900˚С металлическую поверхность. Расплавления основного материала нет, есть диффузия. Сплавление с основным металлом 5-10%.
Преимущества
- Низкая степень перемешивания с основным металлом, что даёт возможность получения необходимых свойств на тонком однослойном покрытии.
- Порошковый материал может быть любого сложного состава с заданными свойствами.
- Низкая стоимость оборудования.
Недостатки
- Пористость покрытия.
- Ограничение по толщине покрытия, до 10 мм.
- Низкое сплавление 5-10% означает также недостаточную прочность.
- Значительные потери материала.
- Низкая производительность, до 1 кг/час.
Ввиду низкой производительности газопламенное напыление целесообразно применять при покрытии малой толщины на небольшие детали.
2.1.2 Электродуговое напыление (ARC-SPRAY process)
Расходным материалом для этого процесса являются две электродные проволоки, которые подаются двумя сварочными источниками в распылитель. В распылитель осуществляется поддув сжатого воздуха. Электрическая дуга между двумя проволоками расплавляет проволоки, а струя воздуха переносит материал покрытия на поверхность детали.
Преимущества
- Низкая степень перемешивания с основным металлом, что даёт возможность получения необходимых свойств на тонком однослойном покрытии.
- Низкий нагрев детали.
- Высокая производительность, до 50 кг/час.
Недостатки
- Пористость покрытия.
- Ограничение по толщине покрытия, до 10 мм.
- Значительные потери наплавочного материала
- Низкое сплавление 5-10% означает также недостаточную адгезию.
Это один из самых экономичных методов при нанесении покрытий на значительные площади, т. е. при больших объёмах работ, ввиду высокой производительности и сравнительной простоте оборудования.
2.1.3 Плазменная наплавка (напыление), (PTA-process).
Для применения этого способа требуется более сложное оборудование.
В данном случае источником тепловой энергии служит ионизированная газовая плазма. Катодом является вольфрамовый электрод, анодами - сопло и наплавляемая деталь. Создаётся дуговой разряд, в который нагнетается газ, он ионизируется и образует плазму. Поток газа увлекает порошок покрытия в плазменную струю, где он расплавляется. В результате достигается высокая концентрация тепла, и порошок интенсивно вплавляется в поверхность детали.
Благодаря этому процессу можно добиться намного лучших результатов. Степень сплавления возрастает с 5-10% до 20-30%.
Преимущества
- Высокая концентрация тепловой мощности и минимальная ширина зоны термического влияния.
- Возможность получения толщины наплавляемого слоя от 0,1 мм до нескольких миллиметров.
- Низкая степень перемешивания с основным металлом (по сравнению с наплавкой), что даёт возможность получения необходимых свойств на первом слое.
- Высокая производительность, до 10 кг/час.
Недостатки
- Высокая стоимость и сложность оборудования.
Это метод позволяет наносить наиболее качественные покрытия и позволяет автоматизировать процесс, поэтому часто применяется при производстве новых деталей, например, наплавка сёдел клапанов в моторостроении.
2.2 Виды электродуговой наплавки.
Один из наиболее эффективных и производительных способов защиты – электродуговая наплавка. Это недорогой и универсальный метод.
2.2.1 Ручная наплавка штучными электродами (РДН).
Преимущества
- Наплавка может проводиться без демонтажа-монтажа сложных и громоздких агрегатов, во всех пространственных положениях и в труднодоступных местах.
- Оборудование простейшее и недорогое.
Недостатки
- Низкая производительность (1 – 4 кг/час).
- Высокие потери наплавочного материала (до 50%). Огарки, брызги, угар.
- Результат по качеству и производительности сильно зависит от «человеческого фактора»- квалификации сварщика.
Ручная дуговая наплавка рекомендуется прежде всего для ремонтной наплавки на единичные изделия сложной формы.
2.2.2 Полуавтоматическая наплавка сплошной проволокой в среде защитного газа (МП).
По сравнению с ручной наплавкой она имеет ряд преимуществ. Так, рабочее время используется эффективнее, поскольку отсутствуют перерывы на замену штучных электродов. При этом сварщик выполняет один непрерывный валик вместо последовательности коротких швов. Нет дефектов, обусловленных зажиганием и обрывом дуги. Меньше потери на разбрызгивание и угар (15-20%). Преимущество по операционному фактору - среднее время использования дуги в смену: 6 часов в смену (у РДН 2 часа в смену). Исходя из сказанного, полуавтоматический процесс наплавки примерно в три раза производительнее ручного и на 30-50 % дешевле.
2.2.3 Полуавтоматическая сварка самозащитной проволокой (МПС).
Наплавка флюсованной или порошковой самозащитной проволокой схожа с наплавкой сплошной проволокой. Отличие в том, что защитный газ 5 не используется. Порошковая проволока содержит флюсующие материалы, которые позволяют вести сварку открытой дугой.
Сохраняя выгодные стороны наплавки сплошной проволокой, этот метод имеет дополнительные плюсы
- При большей стоимости порошковой проволоки удаётся экономить на защитном газе.
- Производительность ещё выше (4-8 кг/час)
- Наплавка может выполняться на открытом воздухе, защиту дуги не сдувает.
Последнее свойство даёт возможность выполнять наплавочные работы без демонтажа и транспортировки в цех деталей крупногабаритной техники.
2.2.4 Автоматическая наплавка проволокой под флюсом (АФПН).
В этом процессе наплавка выполняется либо порошковой проволокой под нелегирующим флюсом, либо проволокой сплошного сечения под легирующим флюсом.
Преимущества.
- Отсутствие излучения и разбрызгивания.
- Высокая производительность (до 15 кг/час).
- Автоматический контроль, стабильное высокое качество.
Недостатки
- Малая универсальность. Каждый автоматический комплекс выстраивается под конкретное изделие.
- Сложное и дорогое оборудование.
Наплавка под флюсом оправдывает себя при больших объёмах повторяющихся работ по покрытию изделий простой формы (цилиндр, конус). Например, наплавка прокатных роликов в металлургии. Опыт работы на многих предприятиях показал, что способ наплавки самозащитной порошковой проволокой, является наиболее экономичным.
3. Выбор наплавочного материала.
Восстановление изношенных элементов оборудования, а также изготовление новых деталей с поверхностным слоем специального сплава можноразделить на три основных этапа.
3.1. Наплавка на поверхность изделия промежуточного, буферного слоя.
Служит:
- для улучшения сплавления слоёв с разными мех. свойствами,
- для развязывания усадочных напряжений,
- для снижения риска «холодных трещин» в основном углеродистом металле.
Для буферного слоя целесообразно применять вязкие аустенитные сплавы системы Железо-Хром-Никель-Марганец (Fe-основа, 19-9-5).
Например, сплошная проволока Kjellberg 4370 MIG, или же порошковая самозащитная проволока для наплавки открытой дугой Corodur 200 OA.
Также зачастую буферный аустенитный слой позволяет снизить степень необходимого подогрева массивных деталей из углеродистых сплавов, который на практике бывает очень трудно обеспечить.
3.2. Восстановление первоначальных размеров изделия (достройка).
Для достройки используют экономичные низколегированные сплавы с достаточной вязкостью и низкой твёрдостью, позволяющие наплавлять неограниченное число слоев. Подойдёт широко распространённая проволока Св08Г2С и подобные. Здесь главный фактор - низкая цена. Если изделие эксплуатируется в условиях не интенсивного износа, этот этап наплавки становится завершающим.
3.3. Покрытия с особыми свойствами.
Самый важный вопрос при борьбе с износом, это вопрос подбора наиболее эффективного состава покрытия с особыми свойствами для придания специальных свойств рабочим поверхностям изделия. Как известно не существует универсальных материалов, успешно противостоящих различным видам износа. В каждом реальном случае нужно выделить преобладающий тип изнашивающего воздействия на рабочую поверхность.
Материалы для износостойкой наплавки можно разделить на ряд групп в соответствии с их хим. составом и стойкостью к различным видам износа.
- Сплавы на основе железа (мартенситные, аустенитные и карбидосодержащие);
- Сплавы на основе никеля и кобальта.
Мартенсит является структурой, образующейся при быстром охлаждении (закалке) углеродистых сталей, легированных Cr. Необходимая твёрдость достигается термическим циклом. Аустенитные сплавы, легированные Ni и Mn обладают ярко выраженным эффектом холодной закалки или наклёпа. Карбидосодержащие сплавы содержат твёрдые карбиды. Свойства, а, следовательно, и области применения, этих материалов различны. Сопоставление их эксплуатационных характеристик только по критерию твердости без учета структуры может быть ошибочным. Например, твердость 50 – 55 НRС могут иметь и мартенсит, и аустенит (после наклепа), и сплавы с карбидами хрома. Однако они показывают стойкость к совершенно разным видам износа. Мартенситные материалы успешно противостоят износу типа «металл по металлу», аустенитные (после наклепа) – ударному, железохромоуглеродистые – абразивному. Максимальное содержание углерода в материале способствует хорошей абразивной стойкости. Увеличение содержания легирующих элементов при неизменном количестве углерода добавляет специальные свойства. Например, материал с высоким содержанием углерода прежде всего имеет хорошую стойкость к абразивному износу. Дополнительное легирование Cr и W позволяет сохранить это свойство при высоких температурах. С другой стороны, дополнительное легирование увеличивает стоимость наплавочных материалов. Сплавы на основе никеля и кобальта противостоят комбинации видов износа, сохраняя эксплуатационные свойства при высоких температурах. Однако они дороги и применение их оправдывается только в тех случаях, когда без этого не обойтись.
3.3.1 Наплавка против фрикционного износа по типу металл-металл.
В этом случае, поверхность не должна быть слишком твёрдой. Обычно достаточно добиться твёрдости в диапазоне 250-350 HB. Требуется высокий коэффициент скольжения, стойкость к давлению и задирам.
Этим свойствам отвечают стали легированные Mn, Сr, Si по 1-2%.
Например, для наплавки применяется проволока 30ХГСА, или проволока Kjellberg 350 MIG. Поскольку эти материалы сравнительно недорогие их выгодно использовать для достройки, то есть восстановления сильно изношенных поверхностей. Применение таких покрытий очень широко: пары скольжения, станины, шестерни, катки, опорные ролики.
В некоторых задачах требуется повышенное скольжение, тогда имеет место покрытие из алюминистых бронз (Cu-основа, Al-7%, Ni-2.5%, Mn 10%).На практике мы это встречаем при восстановлении подшипников скольжения, ползунов и т. д
3.3.2 Наплавка при воздействии давления и сильных ударов.
В этом случае наиболее полезны наплавки из аустенитных сплавов легированные Mn, Ni, Сr с выраженным эффектом холодной закалки. Такие покрытия под воздействием рабочих ударных нагрузок и давления образуют на поверхности наклёпанный слой с твёрдостью до 500HB. Это даёт возможность такой наплавке эффективно противостоять ударам, давлению и незначительному абразиву. Причём важно заметить, что такой слой самовозобновляется в процессе эксплуатации и наплавленные детали обладают большим ресурсом, чем новые детали. Такие покрытия применяются как на низколегированные стали, так и на марганцовистые стали, например, 110Г13Л или сталь Гадфилда. Важная особенность марганцовистых сталей заключается в чувствительности к перегреву выше 300˚С. Поэтому при наплавке необходимо снижать тепловложение и обеспечивать охлаждение детали. Наплавочные материалы этого типа производятся в виде покрытых электродов и порошковой проволоки. Применяются при защите рабочих органов дробилок,опорных роликов, катков, железнодорожных стрелочных переводов. В этих работах показывает высокую эффективность самозащитная порошковая проволока Кородур 250 ОА.
3.3.3 Наплавка при воздействии абразивного износа в комбинации с ударными нагрузками.
Когда основной изнашивающий фактор-абразив требуется высокая твёрдость покрытия. В то же время сплав должен быть достаточно вязким, чтобы выдерживать ударные воздействия. В таком сочетании неплохо работают железные сплавы с высоким содержанием углерода (0.4-0.8%) с добавлением Cr 5-9% и Mo. Покрытие имеет мартенситную структуру с твёрдостью 55-58 HRC и может быть закалена до 60HRC. При наплавке на рубящие кромки гильотин, ножей и зубьев горной техники и т. п. применяются электроды Кьеллберг 6/60 или порошковая проволока Кородур 609 ОА. Наиболее интересны такие решения при восстановительной наплавке роликов и валков прокатных станов в металлургии. Подбор оптимального материала для этих работ довольно сложная задача, требующая учёта комплекса и выраженности изнашивающие факторов, таких как абразив, температуры от 300-900°С, коррозия и высокие давления. Зачастую оптимальный состав удаётся определить после ресурсных испытаний роликов наплавленных различными сплавами мартенситного типа.
3.3.4 Защитные покрытия при интенсивном абразивном износе
Минеральная абразивная среда наиболее интенсивно изнашивает металлические рабочие органы машин. Для защиты разработаны твёрдые сплавы содержащие карбиды -Cr, -Nb, -Мо, -Ti и -W. Твёрдость таких карбидов простирается от 1230HV(хром-карбид) до 3000HV (вольфрам-карбид). В экономичном варианте эти карбиды вплавлены в железной матрице. Более эффективные сплавы на основе Ni-матрицы. Хром-карбидные сплавы получили наиболее широкое применение и позволяют добиться твёрдости 60-62HRC. Например, наплавка электродом Кьеллберг 10/70 содержит Сr-карбиды в железной матрице, а добавление бора (B) позволяет добиться твёрдости 68HRC при двухслойной наплавке. Такие решения достаточно эффективны и экономически целесообразны при борьбе с абразивным износом при значительных объёмах, например молотки дробилок, грохота, лопасти миксеров, шнеки, рыхлители и т. д. В случаях, когда стоимость рабочих частей велика, а объёмы наплавки незначительны, применяются сплавы на основе Ni содержащие сферические карбиды вольфрама. Это позволяет получить бурильные инструменты с твёрдостью, сравнимой с алмазом. Такие решения позволяют многократно продлить ресурс инструментов, технологическая замена которых практически невозможна в процессе бурения, проходки тоннелей и т. п.
Современный подход к вопросам защиты от износа в промышленности включает в себя выбор наиболее эффективного способа нанесения покрытий и подбора наиболее подходящего к данной комбинации изнашивающих факторов материала. Грамотный выбор решения – ключ к успеху в борьбе за стойкость инструментов.
Вольфрамовые электроды для аргоно-дуговой сварки ( ААД, РАД )
Группа компаний «Спецэлектрод Сервис» поставляет на российский рынок вольфрамовые электроды высокого качества для аргоно-дуговой сварки (ААД, РАД) производства «Wolfram Industrie» (Германия).
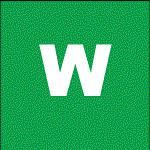
Электрод из чистого вольфрама с содержанием вольфрама не менее 99,5%. Электроды обеспечивают хорошую устойчивость дуги при сварке на переменном токе, сбалансированном не сбалансированном или с непрерывной высокочастотной стабилизацией. Эти электроды предпочтительны для сварки на переменном синусоидальном токе алюминия, магния и их сплавов, так как они обеспечивают хорошую устойчивость дуги как в аргоновой, так и в гелиевой среде. Из-за ограниченной тепловой нагрузки рабочий конец электрода из чистого вольфрама формируют в виде шарика.
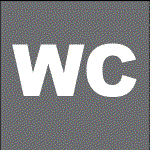
Вольфрамовый электрод легированный 2 % оксида церия (церий— самый распространенный не радиоактивный редкоземельный элемент), который улучшает эмиссию электрода и начальный запуск дуги, так же увеличивается допустимый сварочный ток. Электроды WC-20 универсальные, ими можно сваривать на переменном токе и на токе прямой полярности. По сравнению с чисто вольфрамовыми электродами, электроды с оксидом церия дают большую устойчивость дуги даже при малых значениях тока. Электроды применяются для орбитальной сварки труб, сварки трубопроводов и тонколистовой стали.
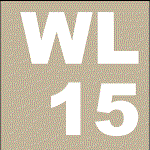
Электроды из сплава вольфрама с оксидом лантана имеют очень легкий первоначальный запуск дуги, низкую склонность к прожигам, устойчивую дугу и отличную характеристику повторного зажигания дуги. Добавление 1-2 % оксида лантана увеличивает максимальный ток, износ электрода на 50 % меньше чем у чистого вольфрамового электрода. Лантановые электроды более долговечны и меньше загрязняют сварной шов. Оксид лантана равномерно распределен по длине электрода, что позволяет длительное время сохранять при сварке первоначальную заточку электрода. Это серьезное преимущество при сварке на постоянном (прямой полярности) или переменном токе от улучшенных источников сварочного тока, сталей и нержавеющих сталей. При сварке на переменном синусоидальном токе рабочий конец электрода должен иметь сферическую форму.
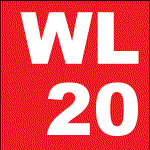
Наиболее распространенные вольфрамовые электроды, поскольку они первые показали существенные преимущества легированных электродов над чисто вольфрамовыми (WP) при сварке на постоянном токе. Тем не менее торий — радиоактивный металл низкого уровня, таким образом, пары и пыль, образующаяся при заточке электрода, могут влиять на здоровье сварщика и безопасность окружающей среды. Сравнительно небольшие выделения тория при эпизодической сварке, как показала практика, не являются фактором риска. Но, если сварка производится в ограниченных пространствах регулярно и в течение длительного времени или сварщик вынужден вдыхать пыль, образующуюся при заточке вольфрамового электрода, необходимо в целях безопасности оборудовать места производства работ местной вентиляцией.
Сварка меди и медных сплавов
Технологические особенности сварки меди и медных сплавов при производстве и ремонте. Специальные легированные электродные проволоки Kjellberg.
Виды медных сплавов
Вследствие недостаточной прочности технически чистую медь применяют редко в качестве конструкционного материала. Широкое распространение в промышленности имеют сплавы меди – латуни, бронзы.
Латунями называют медные сплавы, в которых основным легирующим элементом является цинк. Такие медноцинковые сплавы принято называть двойными латунями. Для повышения механических свойств и химической стойкости латуней в них часто вводят легирующие элементы: алюминий, никель, марганец, кремний и т.д.
Многокомпонентные медноцинковые сплавы принято называть специальными латунями. Сплавы меди с оловом, алюминием, кремнием и другими элементами, среди которых цинк не является основным легирующим элементом, называют бронзами. В зависимости от основного легирующего элемента, различают две группы бронз: оловянные бронзы и специальные бронзы.
Оловянные бронзы, в зависимости от содержания в них других легирующих элементов подразделяют на: оловяннофосфористые, оловянноцинковые и оловянноцинкосвинцовые бронзы.
Специальные бронзы – это двойные или более сложные сплавы на медной основе, содержащие в качестве добавок: алюминий (алюминиевые бронзы), бериллий (бериллиевые бронзы), никель (с добавлением железа – никелевожелезная бронза), марганец (марганцевая бронза), кремний (кремниевая бронза), кадмий (кадмиевая бронза), хром (хромовая бронза).
В зависимости от содержания в алюминиевых бронзах других основных легирующих элементов, их подразделяют на: алюминиевомаргацевые, алюминиевожелезные, алюминиевожелезомарганцевые, алюминиевоникелевые бронзы. Кремнистые бронзы, введением в них марганца или никеля, подразделяют на: кремниевомарганцевые и кремниевоникелевые.
Особенности сварки медных сплавов.
Инертная при обычных температурах медь при нагреве реагирует с кислородом, серой, фосфором и галогенами. С водородом она образует неустойчивый гидрид СuН, с углеродом образует ацетиленистую медь Сu2С2 (взрывчатую); с азотом медь не реагирует, что позволяет азот использовать как защитный газ для сварки чистой меди.
Образование химических соединений переменной валентности и растворимость этих соединений в жидкой меди приводит к довольно сложным диаграммам плавкости и к изменению химического сродства в зависимости от фазового состояния. Медь в условиях сварки может окисляться за счет газовой атмосферы или за счет обменных реакций с компонентами флюсов или электродных покрытий. Сродство меди к кислороду возрастает при растворении закиси меди в жидкой меди, особенно сильно при малых концентрациях Cu2O, и резко снижается до нормального при распаде жидкого раствора в процессе образования эвтектики Сu—Сu2О; Сu2О как отдельная фаза легко восстанавливается до меди. Газы, образующиеся в результате реакций, не растворяются в твердой меди и нарушают металлическую связь между зернами, приводя к образованию трещин - "водородная болезнь" меди.
Твердые растворы меди с кислородом имеют исчезающие малые концентрации при низких температурах. Поэтому медь в процессе сварки необходимо тщательно раскислять или вести сварку в среде инертных защитных газов или в вакууме.
Остаточные концентрации раскислителей влияют на свойства металла шва (электропроводность, теплопроводность, коррозионную стойкость), и поэтому при сварке изделий из чистой меди задача раскисления металла шва решается с трудом.
Остаточные концентрации раскислителей влияют на свойства металла шва (электропроводность, теплопроводность, коррозионную стойкость), и поэтому при сварке изделий из чистой меди задача раскисления металла шва решается с трудом.
К сварным соединениям из чистой меди почти всегда предъявляют высокие требования по сохранению в металле сварных швов всего комплекса физических свойств: электропроводности, теплопроводности, плотности и коррозионной стойкости, так как эти изделия работают в тяжелых условиях эксплуатации. Поэтому в процессе сварки медь не должна загрязняться какими-либо примесями, влияющими на эти свойства.
Механические свойства сварных соединений определяются общими свойствами меди. Сварка чистой меди существенно отличается от сварки сталей.
Большая теплопроводность создает высокие градиенты температуры и скорости охлаждения, а также малое время пребывания сварочной ванны в жидком состоянии. Это обусловливает необходимость применения повышенной погонной энергии при сварке меди по сравнению со сталями или применения предварительного подогрева изделия, но последнее является нежелательным осложнением технологии сварки.
Значительный коэффициент линейного расширения и его зависимость от температуры вызывают необходимость сварки при жестком закреплении изделия или по прихваткам. При большой толщине металла следует регулировать ширину зазора при сварке. Малое время существования сварочной ванны в жидком состоянии ограничивает возможности ее металлургической обработки. В частности, при раскислении меди требуются более активные раскислители, чем при сварке сталей, для снижения концентрации кислорода до допустимых пределов.
Высокие градиенты температуры способствуют развитию термической диффузии водорода в зоне термического влияния, что приводит к обогащению водородом металла вблизи зоны сплавления и увеличивает вероятность возникновения дефектов (пор, трещин). Высокая чувствительность меди к водороду должна учитываться при разработке технологии сварки.
Сварка алюминистых, никелевых и марганцевых бронз идет удовлетворительно даже при использовании ручной дуговой сварки (РДС) специальными электродами, например, Kjellberg 240, производства Германии.
В латунях при этом теряется цинк за счет испарения и окисления. Дуговую сварку в защитных газах, широко применяемую в сварочной технике, используют также для изготовления сварных изделий из меди и ее сплавов, таких как шинопроводы и т. д. Для сварки изделий из чистой меди чаще используют сварку неплавящимся вольфрамовым электродом в среде аргона, гелия или азота. Защитные газы должны быть особо чистыми.
Автоматическую, полуавтоматическую и ручную сварку меди в среде защитных газов можно производить плавящейся проволокой и неплавящимся (вольфрамовым) электродом. Наиболее часто для чистой меди применяют сварку вольфрамовым электродом (для толщин до 10 мм) с подачей присадочной проволоки, реже — сварку плавящимся электродом. Применяют защитные газы: аргон высшего сорта по ГОСТ 10157—73, гелий особой чистоты по МРТУ 6-02-274—66, азот особой чистоты по МРТУ 6-02-375—66. Наиболее целесообразно применять азот высокой чистоты, в котором эффективный и термический КПД дугового разряда выше, чем для аргона и гелия. При сварке в азоте глубина проплавления получается выше, чем при сварке в аргоне и гелии, но устойчивость дугового разряда в азоте ниже, чем в аргоне и гелии.
Однако при сварке в труднодоступных местах или при сварке меди малой толщины ( < 1 мм) предпочтение следует отдать аргону, как защитному газу, в котором наблюдается наибольшая устойчивость дугового разряда. Несмотря на высокую чистоту защитных газов, медь при сварке подвергается окислению, и может возникать пористость, что определяет необходимость применения легированных присадочных и электродных проволок.
Сварку меди неплавящимся вольфрамовым электродом осуществляют на постоянном токе прямой полярности; используют электрод из лантанированного вольфрама, который обладает удовлетворительной устойчивостью в защитных газах, в том числе, и в азоте особой чистоты. При сварке электрод располагают строго в плоскости стыка, наклон электрода 60—80” «углом назад». При сварке меди толщиной более 4—5 мм рекомендуется подогрев до 300—400 °С.При сварке толщин более 6 мм подогрев осуществляют до 850 °С.
Присадочные проволоки из чистой меди М1 и МО при сварке обеспечивают получение металла шва, по составу и физическим свойствам близкого к основному металлу, однако механические свойства сварного соединения понижены, а пористость уменьшает плотность металла шва. При введении в состав присадочных проволок раскислителей и легирующих компонентов механические свойства сварного соединения возрастают, но незначительно, снижаются тепло-и электропроводность металла шва, что недопустимо при сварке ответственных изделий из чистой меди. В таких случаях рекомендуются присадочные проволоки, легированные сильными раскислителями (в микроколичествах), которые после сварки не остаются в составе твердых растворов, а переходят в свои соединения (высокодисперсные, шлаковые включения), и поэтому не влияют на физические свойства металлов. Такие специальные проволоки для сварки меди производятся рядом зарубежными производителями, например, Kjellberg ( Келберг ). Аргонодуговая и азотно-дуговая сварки будут различаться по составу присадочных проволок, так как в азоте возможно образование нитридов некоторыми легирующими компонентами.
Медь толщиной более 5 мм сваривают на флюсовой подушке. Швы большой протяженности сваривают по прихваткам, проставленным с шагом 300—400 мм.
Дуговую сварку латуней и других сплавов меди, содержащих цинк, рекомендуется вести с низкоопущенным соплом. Расход защитного газа зависит от его плотности и теплофизических свойств (л/мин): аргона 8-10, гелия 10—12, азота.
Особенности сварки биметалла медь—сталь, наплавки меди на поверхность стали и сварки меди со сталью.
При осуществлении этих технологических операций возможно возникновение хрупких слоев за счет интенсивного проникновения меди в поверхностные слои стали по границам зерен. Процесс проникновения определяется температурой и временем контактирования жидкой меди с твердой сталью.
Для уменьшения проникновения меди по границам зерен процесс сварки меди со сталью или процесс наплавки меди на сталь надо производить при минимальной погонной энергии и с минимальной глубиной проплавления, используя дополнительное охлаждение для ускорения кристаллизации медного слоя.
Стальную поверхность можно охлаждать со стороны, противоположной наплавке, или охлаждать непосредственно металл наплавки водоохлаждаемыми устройствами.
При наплавке меди в среде аргона плавящимся электродом следует соблюдать аналогичные условия. При сварке меди со сталью плавящимся электродом надо электрод отклонять в сторону меди, так как магнитное дутье в процессе сварки будет возвращать дуговой разряд на свариваемые кромки. При сварке необходимо применять минимальные токи, обеспечивающие формирование сварного шва. Сварку биметалла медь — сталь можно осуществлять со стороны плакирующего слоя или со стороны стали.
В первом случае неизбежны удаление плакирующего слоя на стыкуемых кромках, сварка стали, зачистка полученного шва и наплавка меди на сталь для восстановления плакирующего слоя. При возможности сварки со стороны стали плакирующий медный слой в зоне сварки не удаляют; после сварки стали производят заварку стыка на плакирующем слое любым способом.
Температура подогрева сталей перед сваркой
Таблица значений температуры предварительного подогрева в зависимости от состава сталей и толщины детали.
Наплавляемый металл | Толщина детали, мм | С-экв 0, 3 | С-экв 0,3 – 0,6 | C-экв 0,6-0,8 | 5-12%Cr | >12, %Cr | Нержавеющая сталь | Марганцовистая сталь,≈14 %Mn |
---|---|---|---|---|---|---|---|---|
Низкоуглеродистая сталь | ≤20 20-60 ≥60 ≤20 |
- - 100 - |
100 150 180 100 |
150 200 250 180 |
150 250 300 200 |
100 200 200 100 |
- - - - |
- - - - |
Инструментальная сталь | 20-60 ≥ 60 ≤ 20 |
- 125 - |
125 180 150 |
250 300 200 |
250 350 200 |
200 250 x |
- - - |
о о x |
Хромистая сталь, ≈12 %Cr | 20-60 ≥ 60 ≤ 20 |
100 200 - |
200 250 - |
275 350 - |
300 375 - |
x x o- |
150 200 - |
x x - |
Нержавеющая Сталь | 20-60 ≥ 60 ≤ 20 |
- - - |
100 150 - |
125 200 - |
150 250 x |
*200 *200 x |
- 100 - |
- - - |
Марганцовистая Сталь | 20-60 ≥ 60 ≤20 |
- - - |
- - o- |
*100 *100 o- |
x x o- |
x x o- |
- - o- |
- - o- |
Железохромо-углеродистый сплав | 20-60 ≥60 |
- o- |
100 200 |
200 250 |
*200 *200 |
*200 *200 |
o- o- |
o- o- |
- - отсутствие предварительного подогрева или подогрев до температуры ниже 100°С;
о - предварительный подогрев применяется при большой поверхности детали;
* - для предотвращения растрескивания предварительно наплавляйте промежуточный слой.
Соответствие международных и отечественных стандартов в маркировке сплавов
Маркировка сталей и сплавов, как в ней разобраться ?
Так в России и в странах СНГ (Украина, Казахстан, Белоруссия и др.) принята разработанная раннее в СССР буквенно-цифровая система обозначения марок сталей и сплавов, где согласно ГОСТу, буквами условно обозначаются названия элементов и способов выплавки стали, а цифрами — содержание элементов. Европейская система обозначений стали, регламентирована стандартом EN 100 27. Первая часть этого стандарта определяет порядок наименования сталей, а вторая часть регламентирует присвоение сталям порядковых номеров. В Японии наименование марок стали, как правило, состоит из нескольких букв и цифр. Буквенное обозначение определяют группу, к которой относится данная сталь, а цифры — ее порядковый номер в группе и свойство. В США существует несколько систем обозначения металлов и их сплавов. Это объясняется наличием нескольких организаций по стандартизации, к ним относятся АMS, ASME, ASTM, AWS, SAE, ACJ, ANSI, AJS. Вполне понятно, что такая маркировка требует дополнительного разъяснения и знания при торговле металлом, оформлении заказов и т. п. До настоящего времени международные организации по стандартизации не выработали единую систему маркировки сталей. В связи с этим существуют разночтения, приводящие к ошибкам в заказах и как следствие нарушения качества изделий...
Чтобы всегда иметь при себе верный справочник для сравнения различных стандартов, скачайте документ с подробным их описанием.
Сварка мартенситных нержавеющих сталей
Сварка высокохромистых мартенситных, мартенситно - ферритных и ферритных сталей ручной дуговой сваркой (MMA-SMAW).
В швах по составу аналогичных основному металлу и в зоне термического влияния сварных соединений, выполненных без предварительного и сопутствующего подогрева и последующей термообработки, часто образуются трещины, кроме того, соединения обладают низкой деформационной способностью.
Поэтому в таких случаях приходится отказываться от получения швов, подобных по составу свариваемой хромистой стали. Более работоспособные сварные соединения получаются при аустенитной или аустенитно-ферритной структуре металла сварных швов, обычно хромоникелевых с достаточным количеством аустенизаторов, в основном никеля и марганца. Последующая термообработка по режиму, необходимому для измененного сварочным термодеформационным циклом основного металла, как правило, ухудшает свойства металла шва и вызывает резкие перепады остаточных напряжений вблизи границы сплавления. Поэтому термообработку таких сварных соединений обычно не проводят.
Однако даже при получении швов, подобных по составу основному металлу, необходимо учитывать, что часть наиболее важных свойств сварных соединений может быть получена, когда металл шва по составу несколько отличается от свариваемой стали, например имеет меньшую концентрацию углерода, содержит некоторое количество титана и т.д. В связи с тем, что такое регулирование состава металла шва легче обеспечивается при дуговой сварке, этот способ сварки наиболее распространен при изготовлении и ремонте изделий из высокохромистых сталей. Большинство сварочных работ с этими сталями выполняют ручной дуговой сваркой электродами аустенитного типа с повышенной вязкостью сплава Kjellberg Finox 4370 ( Келберг Финокс 4370 ). Наряду с этим используют полуавтоматическую сварку проволокой Kjellberg MIG 4370, в инертных газах (аргоне, аргонно-гелиевых смесях) или сварку порошковой проволокой Corodur ( Кородур ) под нейтральными флюсами или открытой дугой самозащитной порошковой проволокой Corodur 200 ОА ( Кородур 200 ОА ).
В связи с тем, что растворяющийся при сварке в расплавленном металле водород значительно усиливает склонность к образованию холодных трещин в хрупком металле швов и околошовной зоны, для ручной сварки высокохромистых сталей не следует применять электродные покрытия, содержащие в качестве газообразующих органические соединения. В этом случае используют электродные покрытия фтористокальциевого типа (обмазка основного типа), при которых газовая защита сварочной зоны образуется за счет распада карбонатов покрытия, в основном мрамора.
Образующиеся при этом высококальциевые шлаки благоприятны для удаления из сварочной ванны серы и фосфора - вредных примесей, ограничиваемых в высокохромистых сталях в большей степени, чем в обычных углеродистых. Окислительное влияние газовой фазы (СО2 и продуктов распада) компенсируется использованием электродов, содержащих раскислители в металлическом стержне или чаще в покрытии.
Для уменьшения возможного поглощения водорода электроды перед сваркой следует прокаливать при температуре 450 ... 500 °С течение 2 ч (режим часто приводится в паспорте на электроды). Сварку выполняют постоянным током обратной полярности.
Нержавейка не всегда не ржавеет
Использование пасты травления SE-Paste для послесварочной обработки нержавеющей стали.
Нержавеющая сталь обычно не ржавеет, когда она в нормальных атмосферных условиях. Сопротивление коррозии происходит благодаря образованию на стальной поверхности, тонкого защитного слоя, который предотвращает коррозию. Окисный слой, состоящий главным образом из окиси хрома, называют пассивным слоем, а процесс создания слоя называют пассивацией. Коррозия нержавеющей стали может произойти, когда этот тонкий, защитный слой поврежден, или обеднён хромом, что происходит при перегреве, например, в процессе сварки. Исследования показываю, что коррозия развивается в околошовной зоне после сварки нержавеющих сталей. Особенно быстро появляются очаги питтинговой (точечной) и щелевой коррозии в зоне чёрного цвета и царапин от грубой зачистки.
Таким образом возникает необходимость послесварочной обработки нержавеющей стали. Защитный пассивный слой, может быть восстановлен, если вредный рыхлый оксидный слой, «цвета побежалости», и зону со сниженным содержанием хромом будет снят с поверхности травлением и механической полировкой. Только в этом случае стойкость к коррозии нержавеющей стали будет восстановлена в полной мере. Оптимальным способом послесварочной обработки является травление специальной отбеливающей пастой.
Инструкция по применению SЕ-пасты
SЕ- паста предназначена для очистки травлением поверхности нержавеющих сталей от слоя с дефицитом хрома Cr «цвета побежалости», который образуется при сварке нержавеющих, высоколегированных сталей, а также для травления медно-никелевых сплавов.
Особенность и приемущество: паста розового цвета, что позволяет после ее нанесения видеть обработанные участки и затем качественно смыть пасту после завершения процесса обработки.
Специальные свойства:
Обычно «цвета побежалости» удаляются в течении короткого времени воздействия. СЕ паста легко наносится и хорошо прилипает, что облегчает работу в труднодоступных местах. Раствор пасты не является опасным, т.к. не содержит хлорной кислоты или хлоридов. После травления поверхность стали становится невосприимчивой к окислению.
Применение:
- Поверхность для обработки должна быть охлаждена до комнатной температуры.
- Паста наносится ровным слоем с помощью кисти.
- Время реакции зависит от марки стали и температуры:
- После завершения воздействия обработайте поверхность водой, используя бессолевую воду.
Для нержавеющих сталей 15-60 мин.
Для медно-никелевых сплавов 5-20 мин.
Предостережения:
- CЕ-паста содержит гидрофосфорную кислоту с едким запахом, поэтому рабочее место должно быть хорошо вентилируемым.
- Защищайте пасту от нагрева и солнечных лучей.
- Во время работы используйте защитную одежду для кожи и глаз.
- В случае попадания пасты на кожу немедленно смойте её водой.
Ремонтная сварка чугуна
Сварка чугуна без подогрева. Технология и сварочные материалы Kjellberg Finsterwalde позволяют выполнять надёжный ремонт методом ручной электродуговой сварки деталей из чугуна практически любых марок без подогрева. Исключение составляют лишь высокохромистый и отбелённый чугун.
Разделку трещин при подготовке детали к сварке рекомендуется проводить с помощью специальных разделочных электродов Kjellberg Finsterwalde ( Келберг ). Разделочные электроды позволяют удалять изношенный металл, выжигать масло и примеси из околошовной зоны при малом подогреве детали и с большой скоростью. Производительность при разделке выше, чем при работе абразивным инструментом в 4-5 раз. U-образная разделка, получаемая при работе разделочным электродом по сравнению с традиционной V-образной для абразивного инструмента, позволяет экономить до 25% дорогостоящих материалов для сварки чугуна и сокращает время обработки в 5-10 раз.
Для ремонта чугунных деталей рекомендуется использовать специальные электроды Kjellberg Finsterwalde GRAF ( Келберг ГРАФ ), которые позволяют уверенно проводить сварку, без подогрева и термообработки. Специальные добавки в обмазке электрода обеспечивают формирование углерода в околошовной зоне в форме шаровидного графита. Это исключает риск образования трещин. Замедленное плавление стержня электрода даёт возможность сварки старых и замасленных чугунных деталей. Электрод позволяет сваривать чугун со сталью, никелевыми сплавами и сплавами на основе меди. В особых случаях применяется комбинированная сварка ферроникелевыми электродами Kjellberg Finsterwalde GRAF 4000, плюс электродами на основе никеля Kjellberg Finsterwalde FICAST NI.
Как обойтись без поддува аргона при сварке нержавеющих сталей
Высоколегированная сталь обладает целым рядом преимуществ перед д ругими видами сталей. Прежде всего это коррозионная стойкость и прочность при повышенных и пониженных температурах. Некоторые марки высоколегированных сталей можно использовать в диапазоне температур от минус 190 о С до 500 о С.
Основой высоколегированных сталей является железо с легирующими элементами. Высоколегированные стали подразделяются на три группы:
- Хромистые;
- Хромоникелевые;
- Марганцовистые.
В пищевой и химической промышленности в основном используются хромоникелевые высоколегированные стали как наиболее стойкие к химическому изнашиванию, не реагирующие с пищевыми продуктами и превосходящие остальные группы по механическим свойствам.
Хромоникелевые стали имеют в своей основе железо. Основными легирующими элементами являются хром и никель. Высоколегированные хромоникелевые стали имеют однофазный твердый раствор хрома и никеля в железе в результате чего в них преобладает аустенитная фаза. Ферритной фазы как правило содержится не более 10% в зависимости от содержания хрома. Никель является стабилизатором аустенитной фазы и при содержании в стали более 9% никеля и не более 13% хрома, сталь становится полностью аустенитной, что придает ей пластичность при высоких температурах.
Аустенитные стали обладают высокой прочностью и вязкостью, не ржавеют в атмосфере и морской воде, и проявляют высокую стойкость к коррозии при использовании в кислотах и кислотосодержащих жидкостях.
Нержавеющие высоколегированные хромоникелевые стали хорошо свариваются, однако, имеют специфические особенности при сварке: проявляют склонность к горячим трещинам и межкристаллитной коррозии, а также при недостаточной защите при сварке не дают возможности выполнить надлежащий провар корня шва из-за выгорающего хрома. Сварку высоколегированных хромоникелевых сталей можно выполнять практически всеми способами сварки: механизированным в среде инертных газов, аргоно- дуговым, покрытым электродом. Конечно, при выборе способа сварки для данного вида сталей, преобладает аргоно-дуговой способ. Он зарекомендовал себя как наиболее чистый и качественный. Также, данный способ характерен низким тепловложением, что очень важно при сварке данных сталей.
При сварке трубопроводов из аустенитных хромоникелевых сталей, применяется сварка с поддувом корня шва. Применение поддува обусловлено необходимостью провара корня шва и формирования обратной стороны шва. Кроме того, при поддуве инертным газом снижается степень окисления обратной стороны сварного соединения, в результате чего, снижается склонность к межкристаллитной коррозии околошовной зоны.
Однако, не всегда имеется возможность применения поддува из-за недоступности обратной стороны сварного соединения, будь то ремонтные работы на существующем трубопроводе или сварка глухой конструкции. В таких случаях применяется флюс-паста, которая наносится на кромки обратной стороны шва и при горении образует шлак, защищающий обратную сторону сварного соединения. Данный способ защиты обратной стороны шва имеет недостатки: при неравномерном или чрезмерном нанесении флюс- пасты можно получить недостаточную защиту или зашлаковку корня шва, что приведет к непровару.
Существуют технология с применением специальных сварочных материалов для выполнения сварки хромоникелевых нержавеющих сталей без поддува корня шва и без нанесения флюс-пасты на обратную сторону кромок соединения. По данной технологии корневой проход выполняется специальным материалом, содержащим в своем составе шлако и газообразующие компоненты. В результате этого происходит защита околошовной зоны и сварочной ванны. Последующие проходы выполняются присадкой в виде сплошных прутков. Материал для выполнения корневого прохода марки AWG TF 3016 имеет диаметр 2,2 мм, состоит из стальной оболочки и содержит в себе наполнитель с компонентами рутилового типа. Данный материал может применяться для сварки только корневых проходов хромоникелевых высоколегированных сталей и хромоникелевых сталей с содержанием молибдена до 3%.
автор: Инженер Д. Петров
Изнашивание
В настоящее время при применении различных САПР и расчетных механизмов, а также с учетом использования различных конструкционных и функциональных материалов, практически исключен выход из строя деталей на ранней стадии их работы. В основном, выход из строя деталей машин и механизмов, связан с их неправильным использованием и различными факторами их изнашивания: абразивным, эрозионным, фрикционным, а также различными их сочетаниями.
«Трибология» – наука о трении и изнашивании была учреждена в Великобритании во второй половине 60-х годов 20 века. Там озаботились, почему передовые достижения по снижению износа не востребуются промышленностью. В ходе 2-х летней работы правительственной комиссии было установлено, что в технической среде о них, попросту, плохо осведомлены. Поэтому была введена новая дисциплина – «трибология», которую начали преподавать на всех уровнях. В нашей стране она чаще называется «триботехникой».
Некоторые пары трения изнашиваются довольно длительное время и даже после длительных воздействий не теряют своей работоспособности. Так работают пары трения при фрикционном изнашивании. Здесь также может наблюдаться эффект безызносности, т.е. образования «натира» без образования углублений. Не происходит схватывания поверхности, в результате чего не происходит унос частиц с поверхности более мягкого материала в паре трения. Однако, если рассмотреть абразивное изнашивание в чистом виде, то при недостаточной поверхностной стойкости, в паре трения образуются дефекты, которые мешают использованию механизма, или попросту, делают его использование невозможным или не рациональным.
Если рассмотреть механизм абразивного изнашивания, как наиболее преобладающего в производственных процессах, то можно увидеть, что его вызывают частицы, которые превосходят по твердости изнашиваемую поверхность. Чаще всего это абразивные частицы песка, щебня и прочих природных минералов и керамики. Данные частицы могут внедряться в поверхность, процарапывать канавки, снимать микростружку и всячески уносить частицы изнашиваемого материала или покрытия. Борьба с данным видом изнашивания чрезвычайно актуальна в таких отраслях промышленности, как металлургическая, горнодобывающая, строительная, поскольку данный вид изнашивания является одним из самых быстрых. Для повышения износостойкости конструкций применяются функциональные материалы (бронеплиты, футеровка), а также практикуется нанесение износостойких слоев при помощи различных способов, наплавка, напыление.
При помощи наплавки можно не только упрочнять изнашиваемую поверхность, но и восстанавливать ее с приданием необходимых износостойких свойств. Для наплавки против преобладающего абразивного изнашивания без ударного воздействия может применяться электрод Kjellberg Kait 70 для наплавки износостойких твердых покрытий с включениями карбидов и боридов железа. Наплавленный металл устойчив против воздействия экстремальной абразивной среды в сочетании с высокой температурой (до 500°С). Наплавка имеет высокую твёрдость (60-65 HRC).
Довольно часто на детали, испытывающие абразивное изнашивание, действует и ударная нагрузка в результате чего применение твердых непластичных наплавленных слоев не целесообразно, ввиду их хрупкости. Тогда, в ущерб твердости, необходимо применять материалы, дающие более пластичные наплавленные слои. Таким материалом является Kjellberg Finsterwalde Kait 6000 для наплавки твердых износостойких покрытий с Cr-карбидными включениями. Имеет высокую производительность. Наплавленный металл имеет гладкую поверхность и устойчив к воздействию абразивной среды в сочетании со средними ударными нагрузками.
автор: Инженер Д. Петров